Efficient technology for industry and refrigeration
Plate heat exchangers are essential components in refrigeration and many other industrial applications. They impress with their efficiency and versatility and are indispensable in many sectors. A plate heat exchanger is a specially designed device that transfers heat from one medium to another. Their compact design and high performance make them particularly suitable for industrial plants, the process industry, and in refrigeration technology.
- Features
- Technology
- Applications
- Operating parameters
- Technical data
- Brochures
With API Schmidt-Bretten’s plate heat exchangers, you benefit from innovative technology that combines efficiency, safety and flexibility.
Your advantages at a glance:
- Easy maintenance
The gasket side can be inspected and cleaned as with conventional gasketed plate heat exchangers – uncomplicated and time-saving. - Reduced risk of leakage
Thanks to the ring seal, the seal length is reduced to 20%, reducing the risk of leakage by an impressive 95%. - High degree of flexibility
The modular design allows for easy expansion or modification. Existing gasketed plate heat exchangers can be converted to semi-welded systems. - Fast return on investment (ROI)
No spare parts required on the welded side – this saves costs and significantly reduces downtime. - Cost efficient
Lower costs are required in comparison with purely gasketed plate heat exchangers. Options with FKM or PTFE gaskets offer additional cost-efficiency.
Advanced technology with SIGMADUAL plate heat exchangers
The SIGMADUAL semi-welded plate heat exchangers from API Schmidt-Bretten utilize state-of-the-art laser welding technologies, which guarantee the highest precision and reliability in plate processing.
Special features of laser welding technology:
- Product-side sealing:
Sealing is achieved by precise laser welding around the flow channel and the openings. High-quality elastomers such as nitrile, EPDM, FPM, or PTFE-coated elastomers are also used. - Service-side sealing:
On the service side, elastomers seal the flow channel, while the openings are also laser-welded.
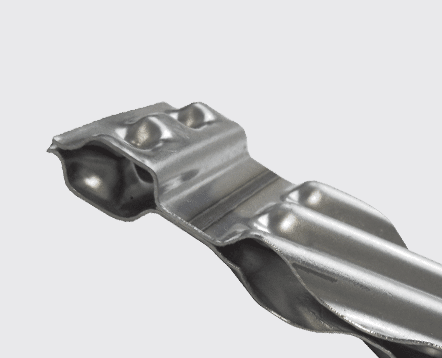

- Industrial markets
- Automotive industry
- Oil and gas industry
- Process industries
- Chemical industry
- Metal processing
- Petrochemical industry
- Refrigeration technology
- Wastewater treatment
Temperature | -29°C – 200°C |
Pressure | Vacuum up to 30 bar |
Volume flows | In excess of 2,000 m³/h |
Connections | DN100, DN150, DN200 and DN350 |
Plates
Standard | AISI 304 (1.4301), 316L (1.4404) |
Special features | AISI 904 (1.4539), SMO 254 (1.4547), nickel alloy, Ti and Ti-Pd alloy |
Gaskets
Standard | Nitrile rubber gasket, EPDM, FPM |
Special features | HNBR, PTFE coated elastomers (SIGMACOAT), FDA compliant materials for the food industry |
Attachment method | SIGMAFIX non-adhesive or glued |
Frame | Enameled carbon steel or stainless steel (solid or as overlay) |
Connections
Standard | Studs, flanges, aseptic, threaded connections in 316L (1.4404) or 316Ti (1.4571) |
Special features | 904L (1.4539), Ti, SMO 254 (1.4547), nickel alloys |
Norms and standards | PED, ASME, ABS, LRS, DNV/GL, BV |
Wir werden gerne persönlich
Kontakt >